Considerations when building a smart big box warehouse.
Warehouse automation and digitalisation are changing the face of the modern warehouse. Now, “big box” warehouse firms must think about future-proofing their facilities to allow for the integration of leading-edge technologies and services – so that they remain competitive in a changing digital world.
The warehouse automation market is expected to triple in size over the next ten years as operators increasingly leverage new, digital solutions to drive efficiencies and optimise operations.
With digitalisation being a decisive source of competitive advantage, firms constructing the next generation of “big box” warehouses must think about the infrastructure necessary to support current and future digitalisation efforts from the very beginning of a project.
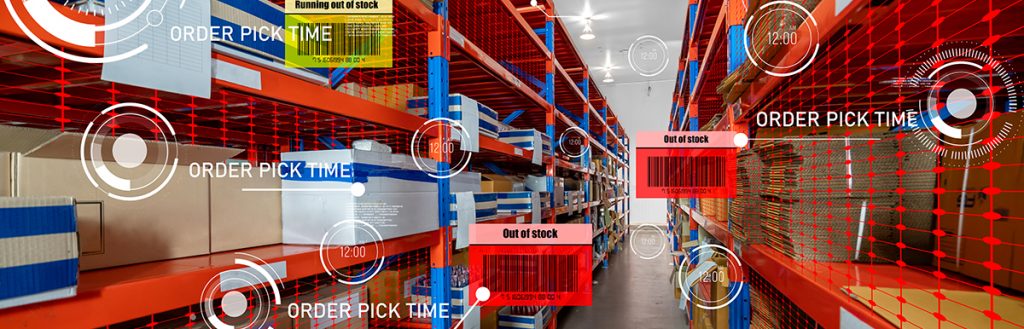
Automation has much to offer warehouse operators. From robotic transportation, picking and packing solutions through to energy efficiency monitoring, digitalisation has a myriad of applications in a modern warehouse.
Innovations which can drive efficiencies and deliver competitive advantage include:
- Sensors, metering and energy management systems to optimise energy use and minimise carbon footprint.
- Intelligent lighting and heating systems to automate energy efficiency measures.
- Integrated renewable energy generation, onsite battery storage systems and electric fleet power and management systems for optimised energy consumption and better energy management.
- Robotics – for forklift trucks, picking, packing and other transport tasks around the warehouse to reduce the reliance on the human workforce, reduce risk and create a safer environment.
- Mobile asset tracking for optimisation of traffic flows around the warehouse as well as asset management and security.
- Automated tagging and tracking systems for a less manual, more “joined up” approach to traceability, tracking and optimisation; reducing the reliance on handheld scanning systems; a more seamless integration with higher-level systems, such as ERP; and reducing the risk of human error.
- Security solutions including keycard and biometric entry systems, cameras, alarms and notifier apps for security inside and outside the warehouse.
- Integrated supply chain solutions for oversight and optimisation across the supply chain.
- Advanced data insights and intelligence – including the development of digital twins – to plot trends, reduce risk, drive efficiencies, predict future requirements, including predictive and preventative maintenance, and to optimise operations.
All of these solutions demand a clear focus on communications, networking and connectivity needed to support them from the very outset of the design and build process, as well as a deep understanding of cyber-security risks and how to mitigate them.
Network connectivity should be planned pre-build
Big box warehouse firms must be thinking about networking and connectivity in the design and planning stages.
The software, data and infrastructure required to deliver and run these solutions are likely to be hosted in the cloud. Cloud offers many advantages in terms of the cost of ownership, scalability, agility, speed of development, cyber security and updating and maintenance of back-end services. It also means that the connectivity to the cloud platforms on which these services are hosted must be high bandwidth, reliable and robust.
Dual points of entry to the building, multiple carriers (with 5G as a backup where this is not possible), failover and resilience and onsite energy storage and/or generation should underwrite the reliability of connectivity.
Inside the building, ethernet cabling, switches, firewalls, routers and other networking equipment must be mapped, planned and budgeted for – ideally to allow for a “plug and play” approach with maximum flexibility and easy expansion offered to tenants as required. The location of this equipment should facilitate resilience and failover capabilities and mapped on a “golden record” of the building plans. The equipment will need to be managed via cloud network management control panels and dashboards with a high degree of automation, including automated backups.
For coverage inside the footprint of larger facilities, mesh networks offer enhanced flexibility, simplified scalability and reliable coverage and connectivity. That’s because, instead of the traditional “hub and spoke” topography of Wi-Fi networks, mesh networking avoids such single points of failure. Nodes can be added easily at any time,
How can brownfield sites keep up?
Whilst retrofitting older facilities isn’t as easy or as cost effective and planning and designing your network infrastructure for the ground up as future-proof and ready for digitalisation, it can be done. Upgrading connectivity and modernising equipment so that it can support a mesh topography will facilitate more simplified expansion of connectivity for digital solutions moving forward.
Considerations when building a smart big box warehouse
For big box warehouse firms, there are many considerations when designing and planning a new facility – not least transportation networks, zoning, local services, the local talent pool, tax and subsidy incentives, as well as the carbon footprint and sustainability of both the build and operationally.
Yet technology plays an increasingly decisive role in the competitiveness of a big box warehouse facility. Thus, technology infrastructure, connectivity and cyber security must be an early consideration in the design and planning of all facilities.